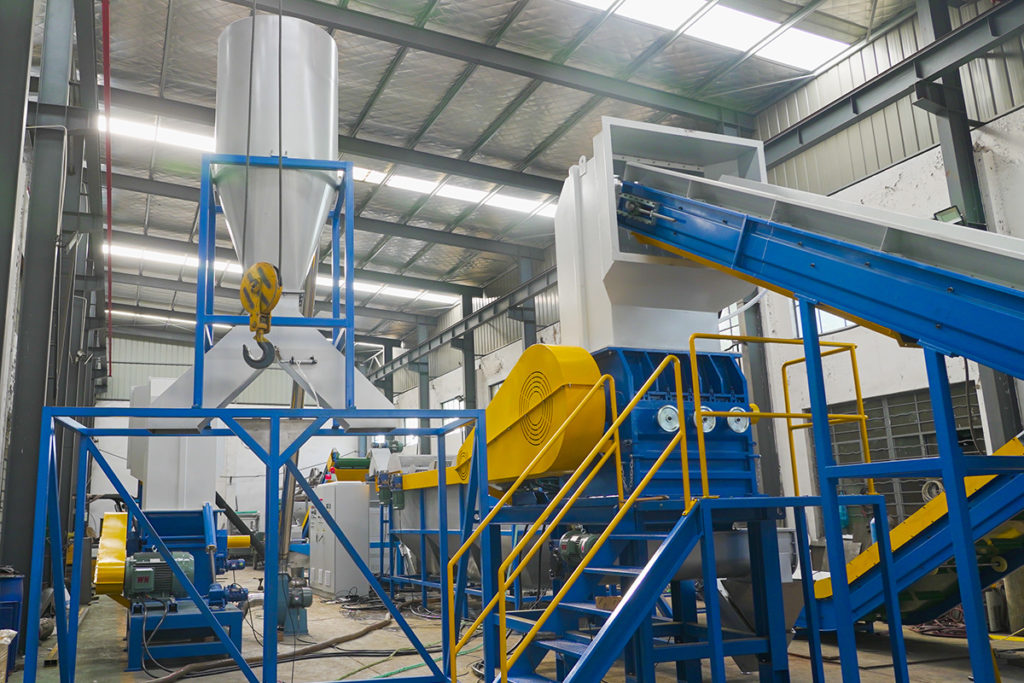
Using densified plastic film for chemical recycling has become the new trend in recycling PE and PP plastic films in the USA and around the world.
Our PP PE film shredding densifying line is your complete solution for turning dirty bales of PP/PE films into densified product ready for chemical application or processing into plastic granules via pelletizing. We offer standard capacities from 200kg/h up to 1000kg/h and can also manufacture as per your requirements.
WORKING PRINCIPLE
- Shredder– As plastic films often come in bales, compacted bundles tied together with wires, the first stage is to breaks the bales using a single shaft shredder with movable hopper. Once the bales are broken, the plastic PP / PE films are shredded and can now drop freely onto the belt conveyor that moves the material onto the next stage.
- Wet Granulator / Crusher – The shredded material is too big for the densifying process. Therefore, the next step is to cut these “shreds” into “flakes”, or small pieces, via our wet granulator. A granulator is made up of an open rotor mounted with heavy-duty knives that spin at high speeds. As the material enter the granulator’s cutting chamber, these rotating knives come into contact with stationary knives cutting the material into small pieces. A screen with small holes between 60-100 mm in diameter is used to control the size of the flakes; That is, the plastic film will continue to be cut within the chamber until it is small enough to fall through the holes on this screen. All the while, water is sprayed into the cutting chamber partially washing the material while acting as a lubricant to reduce friction of the knives and plastic.
- Sink / Float Tank – This is a large tank of water used to clean, wet and remove contamination all at once. As the small pieces of film move along this water tank propelled by large rotating paddles, the plastic film continues to float on top while contamination such as mud/little stones sink to the bottom and are removed.
- Squeezer – This is the most important process in this line where the clean plastic film are densified into irregular pellets using a large screw and heaters. Depending on the material type, the density of finished product is increased dramatically to approximately 350-410 kg/m3.
The densified material after squeezer is around 50 mm long. If this is too large, you can add an additional granulator at the end of the process to reduce its size further.
TECHNICAL SPECIFICATIONS
Capacity | 200 kg/hr | 500 kg/hr | 1000 kg/hr |
Dimension | 25 x 5 x 5.5m | 28 x 6 x 5.5m | 35 x 8.5 x 5.5m |
Operator | 2-3 | 2-3 | 2-3 |
Installation Power | 196 KW | 215 KW | 401 KW |
ADDITIONAL VIDEOS & IMAGES
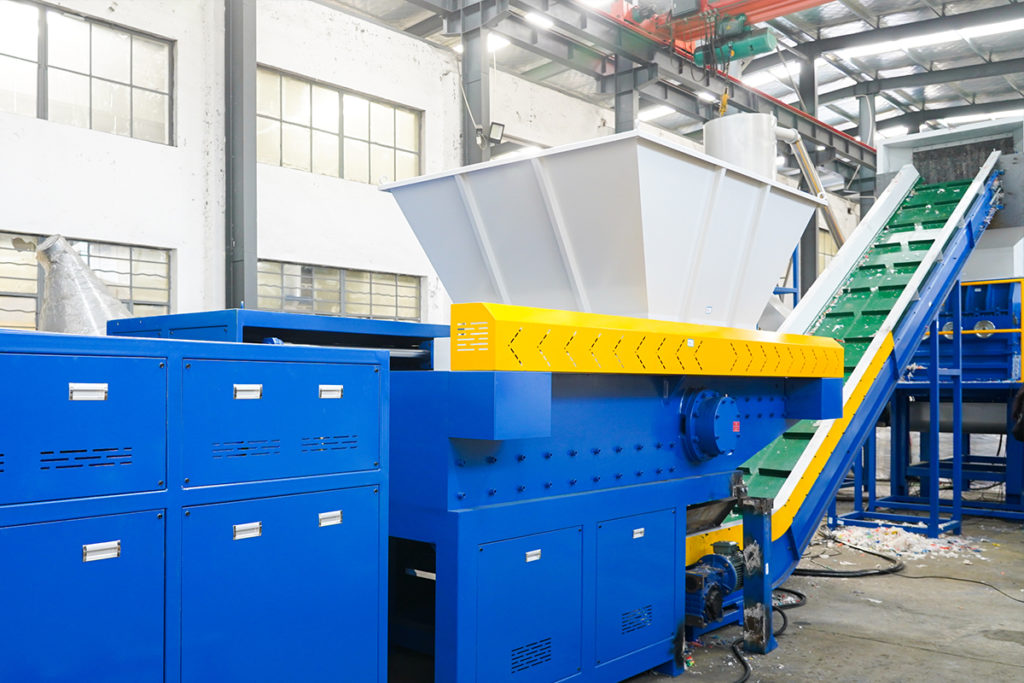
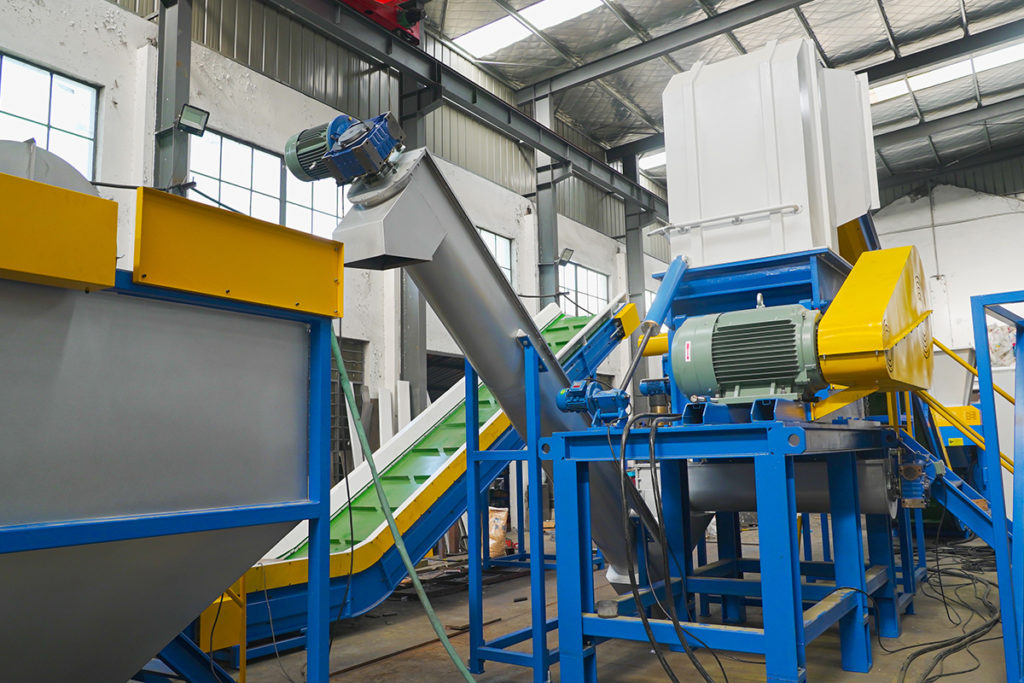
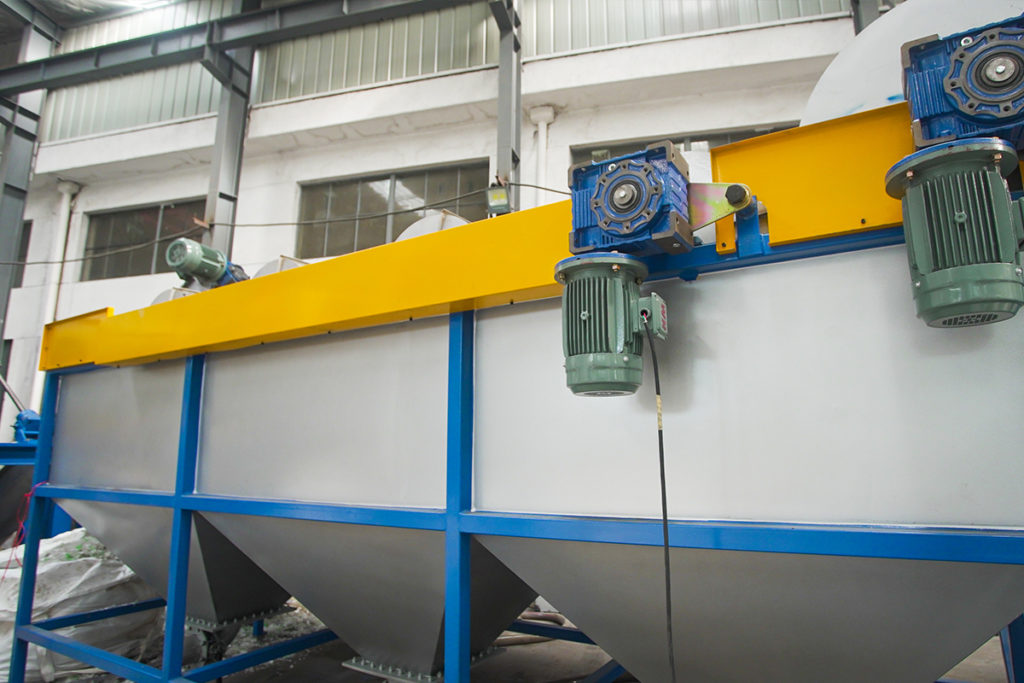
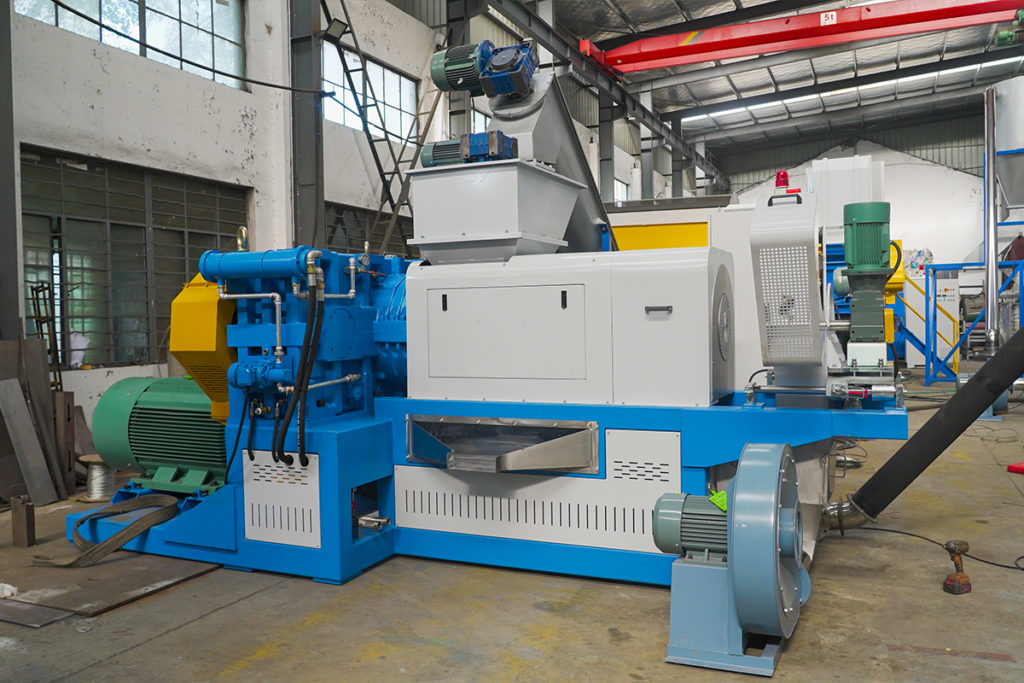
WARRANTY & INSTALLATION
All recycling machinery comes with a limited warranty
We offer installation packages where our engineers travel to your facility to guide your through the installation process the. Routine maintenance teams and operations consultants can also be arranged to ensure your PET recycling plant runs smoothly year and year.
INQUIRIES
To get the latest prices and lead times, send us a message using the form below.