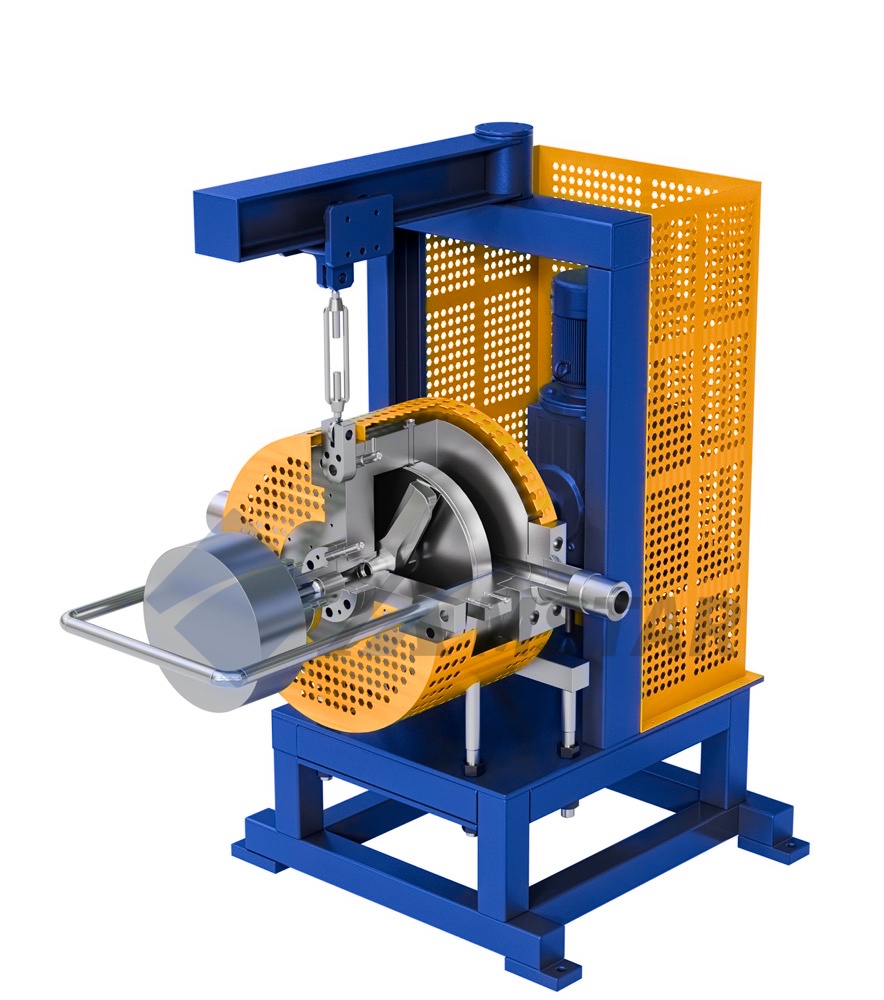
Built for Tough Contaminants. Engineered for Purity.
Amstar’s Laser Filter System is designed to address one of the most critical challenges in plastic recycling: the efficient removal of solid industrial contaminants such as wood chips, paper fibers, stones, metal flakes, and other non-melting residues.
Whether handling post-consumer waste, agricultural film, or rigid packaging, the Amstar Laser Filter ensures stable filtration, high slag discharge efficiency, and minimal material loss—even with the dirtiest input materials.
Key Advantages at a Glance
Feature | Description |
Targeted Impurity Removal | Specially optimized for non-melting industrial solids like wood, paper, and stone. |
Two-Stage Filtration | Integrated coarse + fine filtering in one step — ideal for heavily contaminated materials. |
Self-Cleaning Disc System | Laser-drilled disc filter with continuous or manual/automatic cleaning modes. |
Pressure Monitoring | Equipped with real-time pressure sensors to regulate filter cleaning and avoid clogging. |
Low Waste | Efficient slag removal reduces polymer loss during continuous operation. |
Working Principle
The Amstar Laser Filter employs a rotating disc system featuring laser-drilled micro-holes. As the melt flows across the filter surface:
- Coarse filtration captures larger contaminants like paper and wood.
- Fine filtration ensures downstream equipment receives high-purity melt.
- Slag removal is triggered by pressure thresholds or cleaning cycles, either automatically or via manual control.
This results in continuous, non-stop filtration — no production halt, no manual mesh changing.

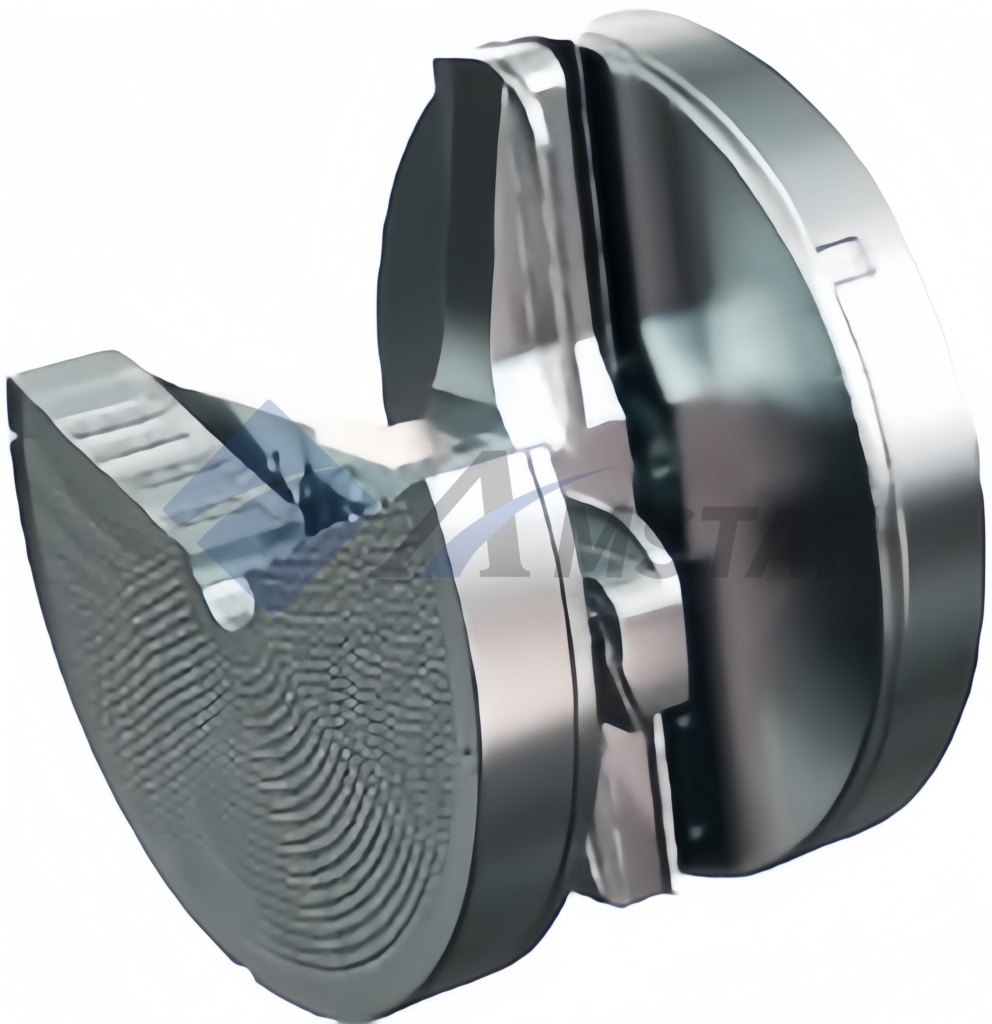
Technical Specifications – Microfilt Disc Filter Series
Model | Disc Diameter (mm) | Filtration Area (cm²) | Capacity (kg/h) |
AMS-400 | Ø400 | 1100 | 200–300 |
AMS-500 | Ø400 | 1700 | 400–500 |
AML-400 | Ø400×2 | 1100×2 | 600–800 |
AML-500 | Ø500×2 | 1700×2 | 1000–1500 |
Mesh Options: 60 / 70 / 80 / 100 / 120 / 130 / 140 / 150
Micron Range: 250μm – 106μm
Why Amstar Laser Filter?
✅ Reliable under pressure – Stable performance even in high-contaminant streams
✅ Fast & efficient cleaning – Disc rotation and pressure-triggered auto-purge
✅ Reduced downtime – No mesh replacement required
✅ Integrated into complete Amstar recycling lines – from washing to extrusionTechnical Specifications – Microfilt Disc Filter Series
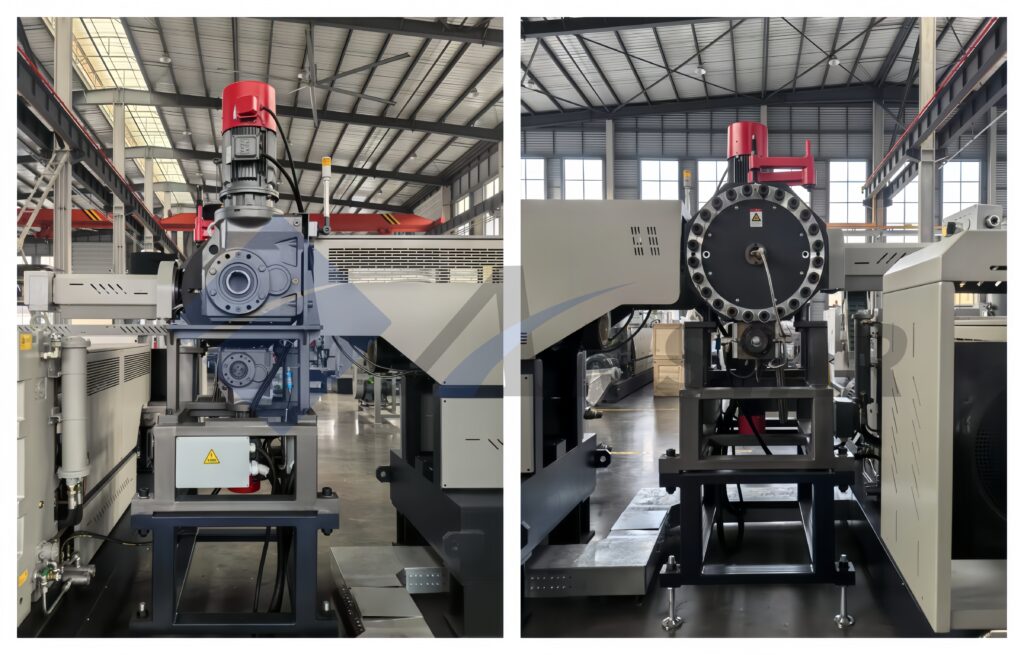
Application Scenarios
• Post-consumer rigid plastic recycling
• Agricultural film with sand, wood, or fiber
• Industrial waste film or woven bags
• HDPE/LDPE film pellets with high impurity content
• Recyclers needing to upgrade filtration for higher-quality pellets
Comparison Chart
• Traditional Screen Changer vs Amstar Laser Filter (Pressure stability / Waste / Downtime)
Feature | Traditional Screen Changer | Amstar Laser Filter System |
Cleaning Mode | Manual screen replacement | Self-cleaning (auto/manual adjustable) |
Operation Mode | Intermittent (requires downtime) | Continuous operation |
Pressure Stability | Fluctuates during clogging | Stable, real-time pressure monitoring |
Material Waste | High during filter change | Minimal due to efficient slag discharge |
Filter Precision Options | Limited mesh range | 250–106 μm (60–150 mesh) available |
Maintenance Frequency | High | Low |
Best For | Lightly contaminated melt | Highly contaminated industrial melt |
Ready to Upgrade Your Filtration?
Whether you need a stand-alone filter or a complete recycling line, Amstar’s engineering team will help you customize the right solution for your application.
INQUIRIES
To learn more about this product, please send us a message using the form below: